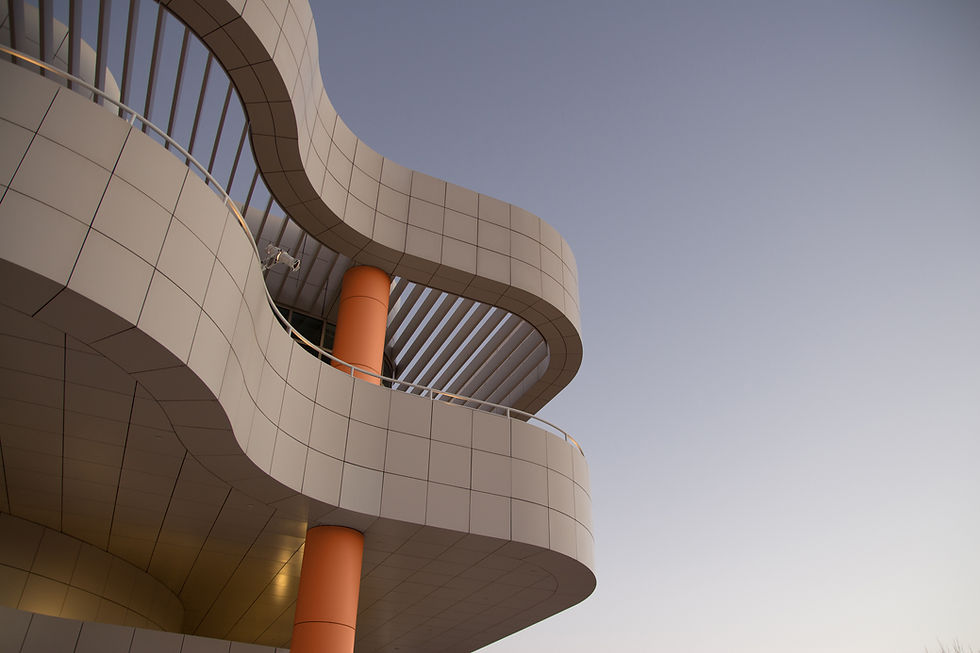
Navigating the Maze: Overcoming Project Delays in Office Fit-Outs in the Philippines
As architects committed to transforming office spaces, we understand the excitement and challenges that come with designing a new workspace. One of the most pressing issues our clients face is navigating project delays. Let’s delve into why these delays occur and how we can collaboratively overcome them to bring your vision to life seamlessly.

Understanding the Problem: Project Delays in Office Fit-Outs
Embarking on an office fit-out project is akin to setting sail on a meticulously planned voyage. Every detail, from design to execution, plays a crucial role in ensuring a smooth journey. However, in the Philippines, one of the most significant challenges we encounter is delays in project timelines. These delays can stem from various sources, each interwoven with the complexities of local conditions and industry practices.
1. Bureaucratic Hurdles and Permitting
Complex Regulatory Environment: The Philippines' regulatory framework, while designed to ensure safety and compliance, can often become a labyrinth for project timelines. Securing permits from multiple government agencies involves navigating a series of approvals, each with its own set of requirements and processing times. For instance, obtaining a building permit from the local government can take anywhere from a few weeks to several months, depending on the project's scale and location.
Compliance Requirements: Ensuring that our designs adhere to local building codes, safety regulations, and environmental standards necessitates meticulous planning. Any oversight can lead to revisions, which not only impact the timeline but also increase project costs. For example, a design initially approved by the Bureau of Fire Protection may require modifications after consultations with the Department of Environment and Natural Resources.
2. Supply Chain Disruptions
Material Shortages: The global supply chain has been volatile, and the Philippines is not immune to these fluctuations. Material shortages, whether due to international trade issues or local production constraints, can lead to significant delays. For instance, a shortage of high-quality steel or specialized fixtures can halt progress until alternative sources are found.
Logistical Challenges: The Philippines, being an archipelago, presents unique logistical challenges. Transporting materials between islands involves coordinating with multiple carriers and navigating through ports that may have their own delays. Additionally, remote areas may experience longer delivery times, further impacting the project schedule.
3. Coordination with Contractors and Subcontractors
Scheduling Conflicts: Aligning the schedules of various contractors and subcontractors is a complex task. Each party has its own timelines and priorities, which can lead to overlaps or gaps in the project phases. For example, delays in electrical installations can hold up the entire fit-out process if not managed effectively.
Quality Control Issues: Maintaining consistent quality across all project components requires diligent oversight. Any lapse in standards by a subcontractor can necessitate rework, leading to additional delays. Ensuring that all parties adhere to the agreed-upon specifications is crucial to maintaining the project timeline.
4. Labor Shortages and Skill Gaps
Availability of Skilled Labor: The demand for skilled labor, particularly in urban centers like Metro Manila, often outstrips supply. This scarcity can slow down specialized tasks, such as intricate carpentry or advanced HVAC installations, affecting the overall project timeline.
Training and Expertise: Ensuring that laborers are adequately trained to execute complex designs is vital. Lack of expertise can lead to errors, necessitating corrections that extend project timelines. Continuous training and upskilling of workers are essential to mitigate this issue.
5. Unforeseen Circumstances
Weather Conditions: The Philippines is prone to typhoons and heavy rainfall, which can disrupt construction schedules and cause physical damage to ongoing projects. Such weather events can lead to temporary halts in construction, necessitating repairs and rescheduling of tasks.
Economic Fluctuations: Changes in economic conditions, such as inflation or currency volatility, can impact project budgets and timelines. Fluctuations in material costs or labor rates may require budget adjustments, which can delay procurement and payment processes.
The Impact of Project Delays: By the Numbers
Understanding the scope of project delays requires a look at the statistics that highlight the extent of the issue:
Philippine Construction Sector Growth: According to the Philippine Statistics Authority (PSA), the construction sector contributed approximately 6.4% to the country's GDP in 2022. However, despite this growth, project delays remain a significant barrier to maximizing this potential.
Permit Approval Times: Data from the Department of Trade and Industry (DTI) indicates that the average time to secure building permits in Metro Manila is around 3-6 months, a period that can extend based on the project's complexity and compliance requirements.
Supply Chain Vulnerabilities: A survey by the Philippine Chamber of Commerce and Industry (PCCI) in 2023 revealed that 45% of construction firms experienced material shortages, leading to delays of up to 20% in their project timelines.
Labor Market Insights: The Labor Force Survey by PSA highlighted that the construction sector faces a 10% labor shortage in urban areas, exacerbating delays in specialized tasks.
Weather-Related Interruptions: The National Disaster Risk Reduction and Management Council (NDRRMC) reported that typhoons in the past five years have caused an average of 2-3 weeks of construction delays per event.
These statistics underscore the multifaceted nature of project delays and the need for comprehensive strategies to address them effectively.
Our Story: Lessons from the Frontlines
Let us share a firsthand experience that encapsulates the challenges and lessons learned from managing project delays.
The Manila Office Revamp
A year ago, we embarked on a project to renovate a sprawling office space in the heart of Makati, Metro Manila. The client, a burgeoning tech startup, had grand visions of a modern, collaborative workspace that would inspire creativity and efficiency. Our design team crafted a plan that seamlessly integrated open office areas, private meeting rooms, and state-of-the-art facilities.
The Unexpected Storm
Just as construction commenced, a severe typhoon hit the region, bringing with it torrential rains and strong winds. The heavy rainfall led to flooding at the construction site, causing significant delays. Essential materials were damaged, and the workforce was unable to continue work safely. The project timeline, initially set for six months, was now at risk of extending by several weeks.
Navigating Bureaucratic Waters
Compounding the weather-related delays were bureaucratic hurdles. The permit renewal process, necessary due to the halt in construction, took longer than anticipated. This delay was a stark reminder of the intricate regulatory landscape we must navigate in the Philippines.
Supply Chain Snags
Simultaneously, our primary supplier faced a material shortage, delaying the delivery of custom fixtures essential for the office design. This shortage forced us to source alternatives, which introduced additional costs and extended the procurement timeline.
Lessons Learned
Proactive Risk Management: We realized the importance of incorporating risk assessments into our project planning. Identifying potential disruptions, such as extreme weather or supply chain vulnerabilities, allows us to develop contingency plans in advance.
Enhanced Communication Channels: Maintaining open and transparent communication with all stakeholders proved crucial. Regular updates and collaborative problem-solving helped mitigate the impact of delays and keep the project on track.
Diversified Supply Chains: Relying on multiple suppliers for critical materials can reduce dependency and enhance resilience against supply chain disruptions.
Streamlined Permit Processes: Building strong relationships with regulatory bodies and initiating permit applications early in the project can help navigate bureaucratic delays more efficiently.
Flexible Scheduling: Incorporating buffer periods into project timelines provides the flexibility needed to accommodate unforeseen delays without derailing the entire project schedule.
The Outcome
Despite the setbacks, the project was successfully completed within an extended timeline of eight months. The final office space not only met the client's expectations but also incorporated improvements based on the challenges we faced. This experience reinforced the value of resilience, adaptability, and proactive planning in overcoming project delays.
How-To Guide: Mitigating Project Delays in Office Fit-Outs
Addressing project delays requires a strategic and collaborative approach. Here’s a step-by-step guide to help us navigate and mitigate the factors contributing to delays in office fit-out projects.
1. Early Engagement with Authorities
Step 1: Research Regulatory Requirements
Begin by thoroughly researching all necessary permits and approvals required for the project. Understanding the specific requirements of local government units (LGUs) and national agencies is crucial.
Step 2: Initiate Permit Applications Early
Submit permit applications well in advance of the project start date. Early engagement with authorities can help identify potential issues that may arise during the approval process.
Step 3: Maintain Open Communication
Establish regular communication with regulatory bodies to monitor the status of permit applications and address any concerns promptly.
Tip: Assign a dedicated team member to manage regulatory compliance and permit acquisition, ensuring that this critical aspect receives focused attention.
2. Robust Project Planning
Step 1: Develop a Comprehensive Timeline
Create a detailed project timeline that outlines each phase of the fit-out process, from design to completion. Include specific milestones and deadlines for each task.
Step 2: Incorporate Contingencies
Build buffer periods into the timeline to accommodate potential delays. This proactive measure allows for adjustments without significantly impacting the overall schedule.
Step 3: Utilize Project Management Tools
Leverage project management software to track progress, assign tasks, and monitor deadlines. Tools like Asana, Trello, or Microsoft Project can enhance visibility and coordination among team members.
Tip: Regularly review and update the project timeline to reflect any changes or unforeseen developments, ensuring that the plan remains realistic and achievable.
3. Diversified Supply Chains
Step 1: Identify Multiple Suppliers
Source materials from a variety of suppliers to reduce dependency on a single source. This diversification mitigates the risk of delays due to supplier-specific issues.
Step 2: Maintain Buffer Stocks
Keep a reserve of critical materials to ensure that production can continue even if supply chains are disrupted. Buffer stocks act as a safety net, providing time to source alternatives if needed.
Step 3: Establish Strong Supplier Relationships
Foster strong relationships with suppliers to enhance reliability and flexibility. Reliable suppliers are more likely to prioritize your orders and accommodate urgent requests.
Tip: Regularly assess supplier performance and have backup options in place to ensure a seamless supply chain.
4. Enhanced Communication
Step 1: Schedule Regular Meetings
Hold frequent meetings with all stakeholders, including architects, contractors, subcontractors, and clients. These meetings facilitate the exchange of updates, address issues promptly, and ensure everyone is aligned with project goals.
Step 2: Utilize Communication Platforms
Implement communication platforms like Slack, Microsoft Teams, or Zoom to enable real-time collaboration and information sharing. These tools enhance transparency and streamline communication.
Step 3: Document Everything
Maintain comprehensive records of all communications, decisions, and changes. Documentation provides clarity and accountability, reducing the likelihood of misunderstandings or disputes.
Tip: Encourage an open-door policy where team members feel comfortable raising concerns or suggestions, fostering a collaborative and proactive project environment.
5. Investing in Local Expertise
Step 1: Collaborate with Local Architects and Contractors
Partner with professionals who possess in-depth knowledge of the local market, regulatory environment, and cultural nuances. Local expertise can streamline processes and enhance project efficiency.
Step 2: Leverage Local Networks
Utilize local networks to access resources, insights, and support that may not be readily available to external firms. These networks can provide valuable assistance in navigating challenges and seizing opportunities.
Step 3: Provide Continuous Training
Invest in training programs to upskill local laborers and ensure they are equipped to handle complex designs and advanced construction techniques.
Tip: Engage in community-building activities with local partners to strengthen relationships and foster a collaborative spirit that benefits the project.
Implementing the Solutions: A Collaborative Effort
Addressing project delays is not a solitary endeavor; it requires a concerted effort from all parties involved. Here’s how we, as architects, can lead this collaborative effort:
A. Comprehensive Project Assessment
Begin by conducting a thorough assessment of the project scope, identifying potential risk factors that could contribute to delays. This assessment should encompass regulatory requirements, material availability, labor resources, and environmental considerations.
B. Strategic Planning and Scheduling
Develop a strategic project plan that outlines each phase, assigns responsibilities, and sets realistic deadlines. Incorporate contingency plans to address unforeseen circumstances, ensuring that the project remains on track even when challenges arise.
C. Proactive Risk Management
Identify potential risks early in the project and develop mitigation strategies. Regularly review and update risk assessments to reflect any changes in project dynamics or external conditions.
D. Transparent Communication
Foster a culture of transparency and open communication among all stakeholders. Encourage regular updates, feedback, and collaborative problem-solving to address issues promptly and effectively.
E. Continuous Monitoring and Evaluation
Implement a system for continuous monitoring and evaluation of project progress. Utilize key performance indicators (KPIs) to measure progress, identify bottlenecks, and implement corrective actions as needed.
Example: Tracking the percentage of tasks completed on time versus the overall project timeline can provide valuable insights into project performance and highlight areas needing attention.
Embracing Technology for Efficiency
Incorporating modern technology can significantly enhance project management and mitigate delays. Here are some ways technology can be leveraged:
1. Building Information Modeling (BIM)
Enhanced Visualization: BIM provides a 3D digital representation of the building, allowing for better visualization and coordination among all parties. This reduces misunderstandings and errors, leading to smoother execution.
Clash Detection: BIM software can identify potential conflicts between different building systems (e.g., electrical, plumbing), allowing for timely resolution before construction begins.
Improved Collaboration: BIM facilitates real-time collaboration, enabling architects, engineers, and contractors to work together seamlessly, reducing the likelihood of delays due to miscommunication.\
2. Project Management Software
Task Management: Tools like Asana, Trello, or Microsoft Project enable efficient task assignment, tracking, and management, ensuring that all team members are aware of their responsibilities and deadlines.
Resource Allocation: These tools help in optimizing resource allocation, ensuring that labor and materials are used efficiently to avoid bottlenecks.
Progress Tracking: Real-time tracking of project progress allows for immediate identification of delays, enabling swift corrective actions.
3. Communication Platforms
Real-Time Collaboration: Platforms like Slack or Microsoft Teams facilitate instant communication, ensuring that all stakeholders are updated on project developments and can collaborate in real-time.
Document Sharing: Easy sharing and access to project documents, drawings, and updates enhance transparency and reduce delays caused by information silos.
4. Drones and Remote Monitoring
Site Inspections: Drones can conduct site inspections, providing high-resolution images and data that help in monitoring progress and identifying issues without the need for physical presence.
Safety Monitoring: Remote monitoring ensures that safety protocols are being followed, reducing the risk of accidents that could lead to project delays.
Fostering a Culture of Flexibility and Adaptability
In an industry fraught with uncertainties, fostering a culture of flexibility and adaptability is paramount. Here’s how we can cultivate this culture:
1. Encouraging Innovation
Promote innovative solutions that address project challenges creatively. Encourage team members to think outside the box and explore alternative methods to overcome obstacles.
2. Embracing Change Management
Implement effective change management strategies to handle alterations in project scope, design changes, or unexpected challenges. Ensuring that changes are managed systematically reduces disruption and maintains project momentum.
3. Building Resilient Teams
Develop teams that are resilient and capable of handling stress and setbacks. Providing training, support, and resources enhances the team's ability to navigate challenges effectively.
4. Prioritizing Continuous Improvement
Regularly assess project processes and outcomes to identify areas for improvement. Implementing lessons learned from past projects fosters a culture of continuous improvement, enhancing efficiency and reducing the likelihood of future delays.
The Path Forward: Collaborative Success
Successfully navigating project delays requires a harmonious blend of strategic planning, effective communication, technological integration, and a resilient team culture. By adopting these strategies, we can transform challenges into opportunities, ensuring that office fit-out projects in the Philippines are completed on time, within budget, and to the highest standards of quality.
Key Takeaways:
Proactive Engagement: Early and proactive engagement with regulatory bodies and stakeholders minimizes bureaucratic delays.
Strategic Planning: Robust project planning with built-in contingencies prepares us for unforeseen challenges.
Diversified Supply Chains: Diversifying suppliers and maintaining buffer stocks enhances supply chain resilience.
Enhanced Communication: Transparent and consistent communication fosters collaboration and timely issue resolution.
Local Expertise: Leveraging local knowledge and networks streamlines processes and mitigates regional challenges.
Technological Integration: Embracing modern technology enhances efficiency, coordination, and monitoring.
Flexible Culture: Cultivating a flexible and adaptable team culture ensures resilience in the face of challenges.
Reflecting on Our Journey
As we continue to navigate the intricate landscape of office fit-outs in the Philippines, we invite you to consider: How prepared are you to adapt and innovate in the face of unforeseen project challenges?